Save Money on Truck Maintenance with Automated Lubrication Systems! (Page 1 of 2)
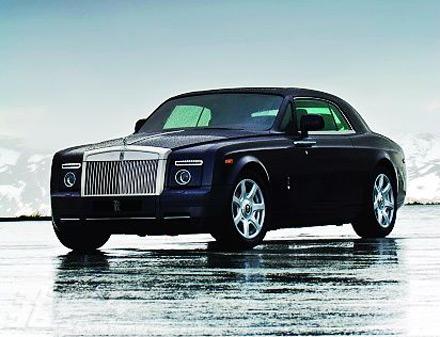
It is always a wise decision to install an automated lubrication system in your fleet of trucks in order to prolong their component life and actually help cut down your maintenance costs over time. Owners can breathe more easily knowing that their trucks components are being greased regularly rather than relying on methods such as point-by-point manual lubrication which is frequently overlooked by operators of the vehicles.
A manual greasing technique requires operators to stop their truck, shut it down and then a mechanic must climb onto/into the truck in order to access the bearings and apply the lubricant by hand. As a result, operators will incur the following results from using a conventional method: increased costs resulting from the fleets downtime; possibly inadvertently overlooking scheduled maintenance; and increased risk for accidents and injuries that can occur while the vehicle is being serviced.
Using an automated lubrication system would be much more effective. Following is information about this operation and the possible benefits to be gained from their usage.
System Function
Generally, using this procedure replaces and eliminates the inconvenience of applying lubricant to the truck bearings and bushings. The procedure has two key functions: First, it does not require the truck to be stopped and shut down, since it is done while the vehicle is in motion; secondly, with this procedure, the greasing maintenance interval will be eliminated. The operators now only have a maintenance interval for the re-filling of the pump reservoir, which fortunately only needs to be done on an occasional basis.
System Installation
This installation is done in a shop qualified to perform such work. All of the procedural components undergo a quality control check and are guaranteed to be repairable and replaceable. The system can be installed on either used or newly-acquired equipment. To ensure the proper operation of it, installation should only be performed by those who have extensive experience in this type of work to ensure that only the right components, up-to-date system design and proper routing of lube-lines will be used on the fleet of vehicles.
System Benefits
The automated lubrication system is one of the best types of preventive maintenance to use, since this type of procedure will significantly reduce a fleets downtime and repair costs. Most fleet owners and operators have taken advantage of using this system as a means of preventive maintenance. When comparing this procedure to the manual lubrication application process, the following list shows some of the benefits that this process can provide for a business:
Typically in the manual application, trucks get greased before or after their operation and the procedure/application would take a minimum of an hour. A fleet with an automated lubrication system is being greased even while it is in operation. Technically speaking, this could increase daily production by an hour, thus reducing overall labor hours.
Leave a Reply