How Diesel tuning systems work… (Page 1 of 2)
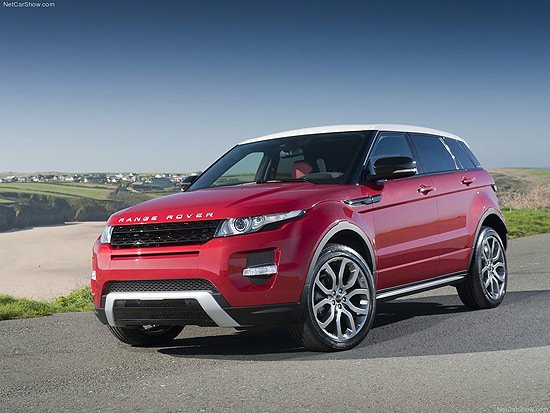
Traditionally the diesel engine was both slow and noisy, suitable only for tractors, trucks and ships, but the trend in recent years has been for high performance diesels to take a large proportion of the car market away from the petrol engine car. Part of this change was the evolution of the high performance turbo diesel, and the popularity of these vehicles has been further improved by a healthy market for performance parts available to the Diesel performance tuning enthusiast. One popular option has been the remapping of the fuel injection and ignition system using a variety of techniques to get the best performance out an engine without resorting to the cost of physically tuning the engine of the car. A factor behind this appears to be the deliberate de-tuning of many cars by the manufacturers, supposedly for reasons of economy, but some say more cynically to leave a niche in the market for higher performance petrol models. Here we take a quick look at how the remapping system works, and the general effects on a typical diesel engine.
A modern diesel engine’s functioning is almost completely controlled by the electronic system that manages the fuel injection and ignition functions. These systems have a number of sensors which are controlled by the vehicles ECU. These signals are processed many thousands of times each second to keep the vehicle running at its optimum efficiency, and also to keep the engine’s emissions at acceptable levels. The idea behind a diesel tuning box is to intercept the signal between the ECU and the injection system, and basically allows it to inject a more optimal amount of fuel into the cylinders thus producing more torque and power. Because of this the engine runs more efficiently. Fuel economy is also improved because you would have to use less throttle to achieve the same performance level, and because the engine is tuned to burn its fuel more efficiently. To understand how the tuning box works it is important to understand the workings of a diesel engine.
In a diesel engine it is only air that is drawn into the compression cylinder. This is then compressed and reaches a very high temperature. When the piston is nearing the top of its stroke fuel is injected into the combustion chamber and ignites due to the high temperature of the air. This creates the power to drive the piston down, turning the crankshaft and wheels. Often there is unused air left in the cylinder after the combustion completes: sometimes as much as 50% of what was drawn in to the engine. Simply speaking when the correct amount of extra fuel is injected into the chamber more torque and power and is created. The ìcommon railî is the central container which delivers the individual injectors with the fuel. The three essential components of a fuel injection system: Pressure, injection and generation are separated, and fuel can be stored at high pressure in the ëcommon railí container. This allows high injection pressure even at slow speeds and provides a fine atomisation of the fuel, which gives a cleaner combustion. The supply of fuel is not related to the engine speed as it is controlled independently at every point along the way improving efficiency.
Leave a Reply