Essential Components in a Hydraulic Press Brake
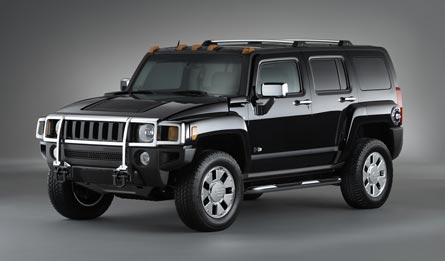
The intention behind using a press brake is to bend metals. Heavy metals as will as thin metals can be manipulated by the use of mechanical press brakes and by hydraulic press brakes. More often than not, a person will decide upon the hydraulic press brake because it is able to apply more pressure, more than 50,000 metric tons actually. Hydraulic press brakes are best suited for any job that is in need of steady pressure in the stroke, or in the different lengths of the stroke, and in the high or changing forces. To better comprehend what a hydraulic press brake does, you should first learn how it performs. Because hydraulic press brakes are complex, we have broken down some of the components that are essential to its function.
Component No. 1 The Hydraulic Fluid Hydraulic fluid moves through different parts of the system because of the high pressure pushing it along. This fluid, as a result, is highly energized. The purpose of it traveling through the system is to transfer all the energy created to the cylinder, which then takes that fluid with its energy to the piston. At this time, the metal is bent and the fluid is moved back into the hydraulic pump where it will once again become energized. The hydraulic fluid is usually petroleum oil among other elements.
The hydraulic fluid also cleans out all unwanted contaminants and lubricates the components of the hydraulic press brake. The hydraulic fluid should be capable of operating at high temperatures, including a few hundred degrees Celsius, as it gets heated when it receives the energy in the hydraulic pump.
Component No. 2 Hydraulic pump The hydraulic pump provides power for the hydraulic fluid to become energized and then sends the fluid on to the cylinders and pistons. To determine how much the hydraulic pump can handle, look at its rating; 5,000 psi can keep up the flow of liquid against the loads of 5,000 psi or, alternatively, it can apply the same degree of pressure. The hydraulic motor power density is ten times more than the power density in an electric motor. The hydraulic pump is activated by an electric motor or an engine connected by gears, belts, or flexible couplings. A gear pump, vane pump, axial piston pump, or a radial piston pump can be responsible for the operations.
Component No. 3 Actuator The hydraulic fluid drops off its energy at the actuator and the energy then makes it press. Actuators vary, but the one that is used in this particular system is the hydraulic cylinder, which is made up of the cylinder barrel and a reciprocating piston. A great amount of energy is in the hydraulic fluid, all of which is sent to the piston to allow for the pressing of the metal sheets. The pistons stroke length should be programmed appropriately to the thickness of the metal sheet and to the angle of the bend. The cylinder length defines the length of the stroke. Accurate control of the pressure of the piston is determined by the stroke. The speed can be made to vary or it can be made to stay the same. The hydraulic cylinder makes up the “motor” side of the hydraulic press brake system.
Component No. 4 Control valves The control valves determine the amount of hydraulic fluid that each actuator receives, including the amount of energy. In accordance with the requirements of operation, fluid is evenly distributed among the control valves when there are multiple actuators.
Once again, the four main components are the hydraulic fluid, hydraulic pump, the actuator, and the control valves. These work together to make a hydraulic press brake system, of which you should now have a basic understanding.
Leave a Reply