Drivers are at Risk from Malfunctioning Tires (Page 1 of 2)
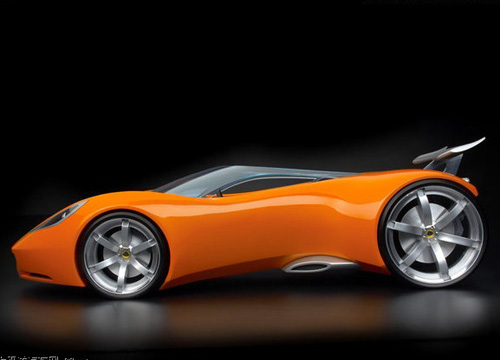
Tire failure has been the cause of more than 8,000 serious traffic accidents yearly, according to the National Highway Traffic Safety Administration. These accidents have either caused serious injuries, or even death. This statistic is frightening as most of these tire failures put the manufacturers directly at fault. These could be due to some manufacturing or possibly design defect. Drivers are often unaware of the dangers of defective tires, despite the fact that manufacturing companies may be familiar with the instability.
Tread Separation Causes Fatal Accidents
One of the most common tire failure occurs due to tread separation. Tread separation is the result of the plies of a tire separating from one another.
An assembled tire is exposed to high temperatures and pressure to cure the assembly, which bonds all the layers. A steel-belted radial tire may have a steel belt incorporated into it to have greater puncture and impact resistance. Unfortunately, the rubber compounds cannot stick to the steel belt addition if the manufacturer does not cover the steel wires before using them in constructing the tire, which makes it possible for tread separation in all steel belted tires. The possibility of tread separation becomes greater as the speed of the vehicle increases.
Currently, light truck tires and passenger tires do not use new technology that has been designed to prevent tread separation from occurring. This new way to manufacture tires has been available for years, but it has not been used because it adds expenditures to production. With better-designed tires, a nylon cap adds a layer between the steel belt and the road to help the tire better withstand moisture and roll with more stability.
Multi-Piece Rims Pose a Serious Threat
Another type of tire failure that can occur is when a multi-piece wheel is used. The Occupational Safety and Health Administration wanted to ban multi-piece rims, but the tire and wheel industry sponsored an education program at work and ultimately avoided the ban. OSHA guidelines require using a safety cage during tire mounting operations, but after the wheel is removed from the safety cage, accidents still happen. Posters that were designed for the education program are now in most service stations and tire shops, but this educational program has allowed manufacturers to avoid complete liability by foisting some liability on to businesses, who in turn pass costs along to employers and their injured employees. Though a single piece wheel that would avoid multi-piece rim explosions has been around for decades, the design has not been widely used.
Sidewall Zipper Failure
When tires are being inflated, the sidewall of the tire can explode, causing a sidewall zipper failure. Sidewall zipper failures can happen because of the design and manufacturing of the sidewall. Deflating a tire can add stress when the tire is re inflated and cause a blowout. Manufacturers deal with this tire failure by issuing warnings instead of changing the tire designs. Bead failures also occur during the inflation of the tire, and the explosion bead failures cause often times result in serious and deadly conditions. Bead fractures usually occur at the splice joint of the tire, which, combined with the low-pressure explosion, causes the trajectory of the rim and the tire to sever limbs, cause brain trauma, and smash facial bones. High-speed spin-off failure can also be a cause of tire failure. This happens when one of the two back wheels remains immobile while the other one spins uncontrollably, which is due to a defect in the design. One uncommon type of tire failure is ozone cracking in which small cracks on the rubber’s surface come from atmospheric ozone which destroys the sidewalls. Manufacturing defects are normally to blame in cases of ozone cracking.
Leave a Reply